Built Engine Update: Addressing Main Cap Instability in the Nano EcoBoost
Following the impressive dyno results of the first-ever "built" Nano EcoBoost, producing 709 AWHP and 675 ft-lbs of torque, the engine encountered unexpected issues. After making changes to bolt-on components to extract more power, a critical problem arose—once the engine reached operating temperature, it would no longer crank when hot.
Diagnosing the Issue
Our partners at Nostrum spent over two weeks thoroughly investigating the problem. Every possible factor was examined. While not an exhaustive list of what was explored, it was ensured that: a new starter was installed, the electrical system was inspected, the oil was drained to check for metal contaminants, and the transmission and torque converter were verified as free of defect or damage. With no significant findings, the hot-start failure symptom remained. The only options left were to either disassemble the engine and transmission further for a full teardown, or to continue testing the car until additional symptoms developed. The decision was made to proceed with testing.
Eventually, the engine began producing metal shavings, giving us a clearer direction for further analysis.
Root Cause Analysis
For those unfamiliar with our process, we do not assemble our built engines in-house. Instead, a specialized machine shop handles the entire long-block, from machining to final assembly. Upon returning the engine to the machine shop for a comprehensive failure analysis, the root cause was identified: excessive main cap movement due to stretching of the main bolts under high torque loads.
This issue was anticipated to some extent, as we had long suspected the main caps would be a limiting factor in the platform. However, we did not expect the problem to manifest at this stage.
Upon close examination of the fractured main caps, the evidence was clear. One cap displayed a dull fracture line with a properly seated cap, while another showed significant polishing and galling—strong indications of cap movement. This not only explains the symptoms observed in this engine but may also shed light on a handful of broken crankshaft failures reported in similar builds.
A Path Forward
After consulting with our machine shop, we explored various solutions, including upgrading to stronger studs. However, it quickly became evident that additional reinforcement was necessary. By examining different variants of this engine in both CAD models and physical components, we identified a potential solution based on observations of the F150, Ranger and Bronco nano blocks that we have on hand.
The 3.0L Explorer variant employs a two-piece crank girdle design with a sheet-metal weldment that ties into the outer main bolts. However, this design leaves the crank mains insufficiently supported. If you look at the upper block without the lower block on, you can see that the mains are effectively "hanging" in place (other than the 2 bolts that tie it in to the lower block). In contrast, the 3.0L Nano engine used in the Bronco Raptor integrates the main caps directly into the lower block structure, significantly improving stability.
To address this, we designed a one-piece steel girdle to unify and reinforce the main caps. This, combined with main studs and upgraded ARP outer bolts, provides the best possible support for the crankshaft. Using a combination of CAD modeling and 3D printing, we iterated through multiple design variations before finalizing the optimal configuration.
The prototype is currently in the machining phase, after which it will be sent to the machine shop for final fitment and assembly. One of the primary challenges with this upgrade is the fractured main cap design, which prevents us from simply cutting down the main cap and line-bore resizing the mains. Fortunately, our partner machine shop was able to find bearings that allow line boring and honing of the mains to compensate for bore distortion when the main studs are torqued down with the girdle.
Moving Forward
We understand that this update has been long-awaited, but we wanted to ensure a viable solution was in place before presenting our findings. Should this approach prove ineffective, we have contingency plans ready to implement.
We remain committed to pushing the boundaries of the Nano EcoBoost platforms and will continue refining our solutions to enhance reliability and performance. Thank you for your patience and support—we look forward to sharing further updates soon.
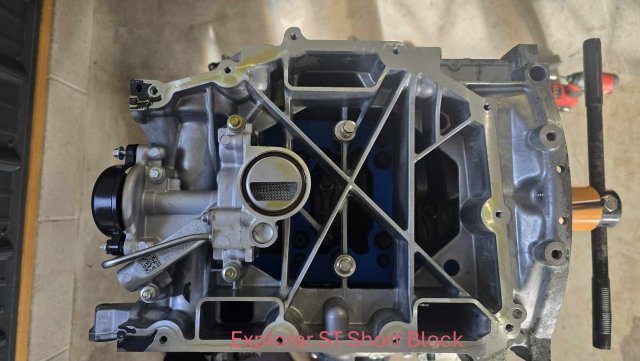
Following the impressive dyno results of the first-ever "built" Nano EcoBoost, producing 709 AWHP and 675 ft-lbs of torque, the engine encountered unexpected issues. After making changes to bolt-on components to extract more power, a critical problem arose—once the engine reached operating temperature, it would no longer crank when hot.
Diagnosing the Issue
Our partners at Nostrum spent over two weeks thoroughly investigating the problem. Every possible factor was examined. While not an exhaustive list of what was explored, it was ensured that: a new starter was installed, the electrical system was inspected, the oil was drained to check for metal contaminants, and the transmission and torque converter were verified as free of defect or damage. With no significant findings, the hot-start failure symptom remained. The only options left were to either disassemble the engine and transmission further for a full teardown, or to continue testing the car until additional symptoms developed. The decision was made to proceed with testing.
Eventually, the engine began producing metal shavings, giving us a clearer direction for further analysis.
Root Cause Analysis
For those unfamiliar with our process, we do not assemble our built engines in-house. Instead, a specialized machine shop handles the entire long-block, from machining to final assembly. Upon returning the engine to the machine shop for a comprehensive failure analysis, the root cause was identified: excessive main cap movement due to stretching of the main bolts under high torque loads.
This issue was anticipated to some extent, as we had long suspected the main caps would be a limiting factor in the platform. However, we did not expect the problem to manifest at this stage.
Upon close examination of the fractured main caps, the evidence was clear. One cap displayed a dull fracture line with a properly seated cap, while another showed significant polishing and galling—strong indications of cap movement. This not only explains the symptoms observed in this engine but may also shed light on a handful of broken crankshaft failures reported in similar builds.
A Path Forward
After consulting with our machine shop, we explored various solutions, including upgrading to stronger studs. However, it quickly became evident that additional reinforcement was necessary. By examining different variants of this engine in both CAD models and physical components, we identified a potential solution based on observations of the F150, Ranger and Bronco nano blocks that we have on hand.
The 3.0L Explorer variant employs a two-piece crank girdle design with a sheet-metal weldment that ties into the outer main bolts. However, this design leaves the crank mains insufficiently supported. If you look at the upper block without the lower block on, you can see that the mains are effectively "hanging" in place (other than the 2 bolts that tie it in to the lower block). In contrast, the 3.0L Nano engine used in the Bronco Raptor integrates the main caps directly into the lower block structure, significantly improving stability.
To address this, we designed a one-piece steel girdle to unify and reinforce the main caps. This, combined with main studs and upgraded ARP outer bolts, provides the best possible support for the crankshaft. Using a combination of CAD modeling and 3D printing, we iterated through multiple design variations before finalizing the optimal configuration.
The prototype is currently in the machining phase, after which it will be sent to the machine shop for final fitment and assembly. One of the primary challenges with this upgrade is the fractured main cap design, which prevents us from simply cutting down the main cap and line-bore resizing the mains. Fortunately, our partner machine shop was able to find bearings that allow line boring and honing of the mains to compensate for bore distortion when the main studs are torqued down with the girdle.
Moving Forward
We understand that this update has been long-awaited, but we wanted to ensure a viable solution was in place before presenting our findings. Should this approach prove ineffective, we have contingency plans ready to implement.
We remain committed to pushing the boundaries of the Nano EcoBoost platforms and will continue refining our solutions to enhance reliability and performance. Thank you for your patience and support—we look forward to sharing further updates soon.
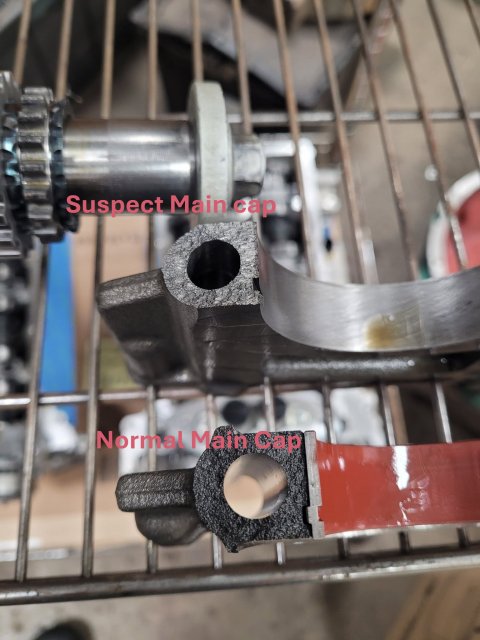
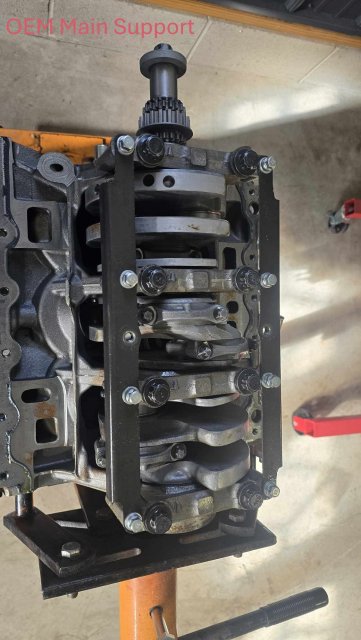
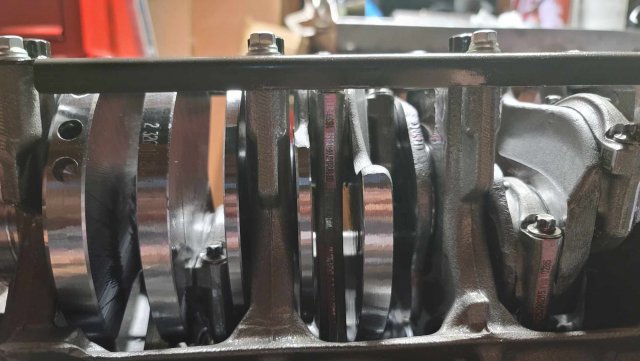
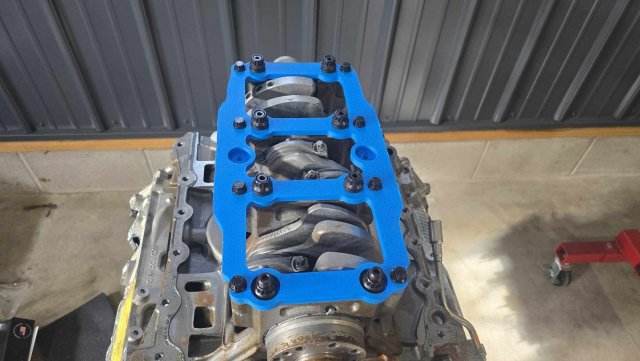
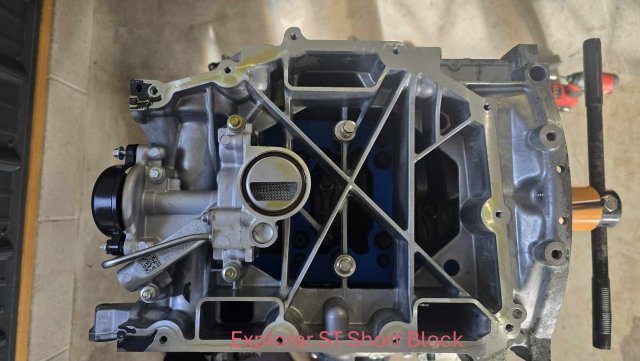
Attachments
-
223.4 KB Views: 15
-
171 KB Views: 15
-
174.3 KB Views: 19
-
150.7 KB Views: 22
-
149.1 KB Views: 23
-
7
- Show All